Bollman Hat Company turns to mask making to bring its factory back to life
by Karen Kahn
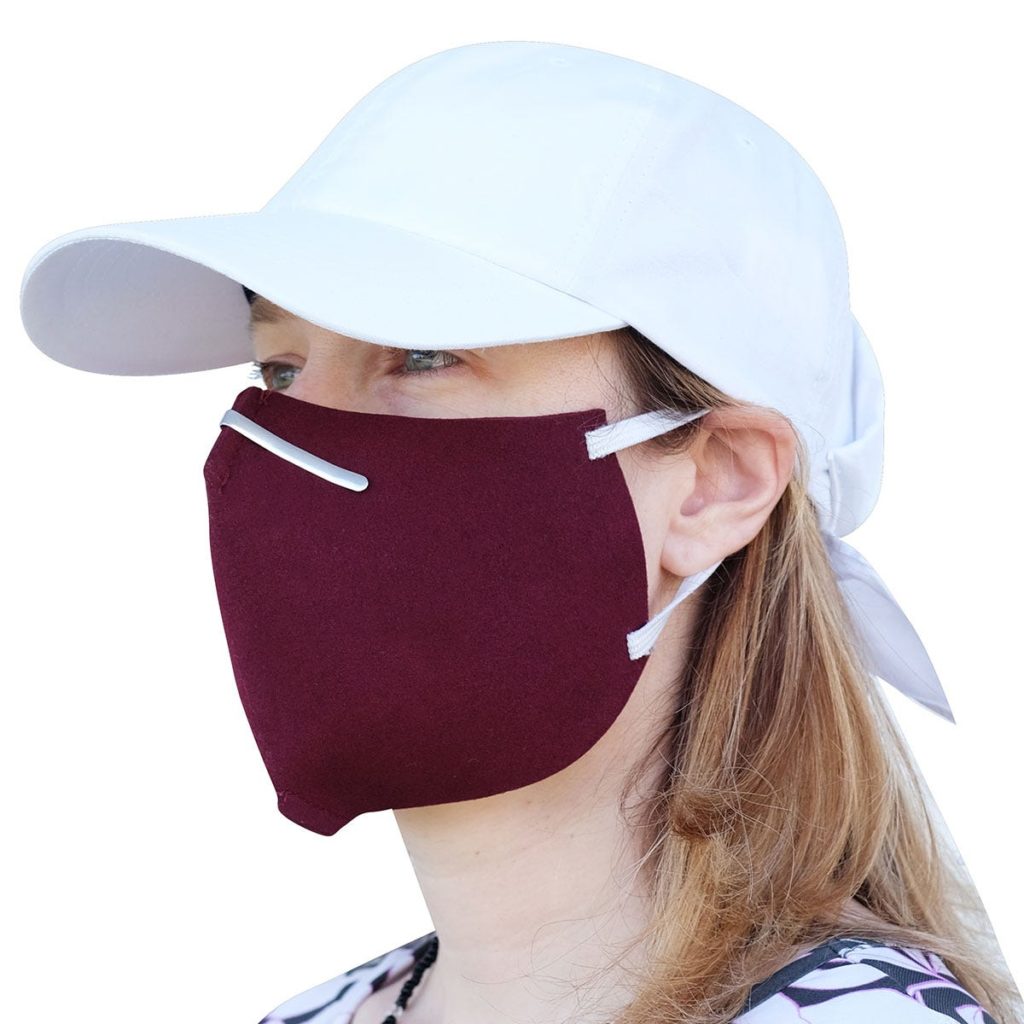
These days, at hats.com you can find more than hats for sale. How about a pack of multi-colored wool felt facemasks? Made by Bollman Hat Company, the oldest hatmaker in the U.S., the facemasks are made from leftover materials that are carefully measured and washed in their Adamstown, PA, factory, which was closed down on March 19. Now the factory is back open, with a slimmed down workforce of 25 making protective face wear that we all need to reduce the spread of COVID-19.
Bollman didn’t go into the business of making masks for the money—about a third of the masks have been given away to homeless shelters, soup kitchens, and other local charities. For this employee-owned firm, producing facemasks was a way to get some of their employees back to work while also contributing to their community. It’s a small act of kindness that grows out of a culture of caring and stewardship: caring for employees by providing quality employment and stewarding the firm by ensuring that each generation leaves the company stronger for those who inherit it.
That’s a tough mission in today’s world, with a worldwide economy on hold. But Bollman Hat Company has some advantages, particularly a strong employee-ownership culture. That, says Kevin McPhillips, CEO of the Pennsylvania Center for Employee Ownership, is the variable he sees as most important to a firm’s success in today’s troubled economy.
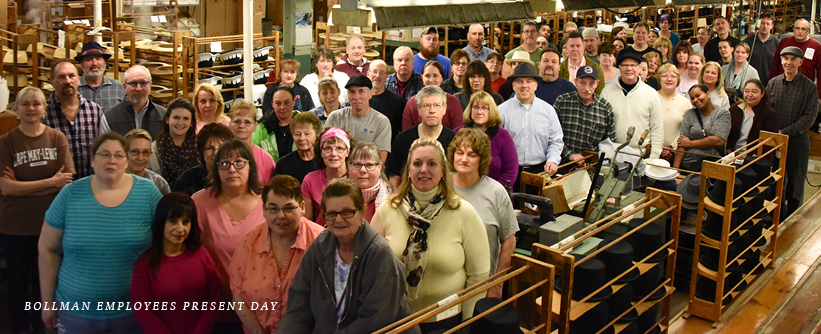
With employee ownership, people care more and give more, and that ensures that more employers can make it through tough times.”
–Don Rongione, CEO of Bollman Hat Company
The Bollman Hat Company was founded in 1868 in Adamstown, PA. Family-owned and -operated for generations, the firm was sold to a group of managers in 1974. In the early 1980s, when Don Rongione, now the firm’s CEO, arrived on the scene, the owners were in search of a succession plan. Rongione recommended selling the firm to the employees through an ESOP trust. He says, “I found a caring culture that was a good match for employee ownership. We launched the ESOP in October 1985, and I firmly believe the ESOP and our ownership culture is, in large part, what has made it possible for us to survive all these years.”
Notably, Rongione points out, Lancaster County used to be littered with hatmakers, but only Bollman Hat Company and one other has survived into the 21st century. He explains that the current pandemic is only one of the serious economic disruptions the company has endured: in the early 2000s, most-favored nation status for China opened up new competition, and in 2008, the Great Recession took the wind out of the consumer economy. At each of these moments, the deep engagement of the employee-owners has made a difference. Rongione turns to his version of a common metaphor to describe the importance of employee ownership at his firm: “No one ever changed the oil in a rental car,” he says. “As owners of Bollman Hat Company, our employees do more than that; they are the oil that keeps this vehicle going.” He’s got a well-oiled machine.
Nonetheless, Bollman Hat Company may be facing the most serious economic crisis of its long history. Not only did the Adamstown factory have to shut down on March 19, per order of the state’s governor, but most of the retailers around the world who sell the firm’s many hat brands (e.g., Kangol, Helen Kaminski , Bailey and others are also closed. Bollman’s wool scouring plant in Texas (which remains open) and e-commerce produced only 11 percent of the firm’s revenue in 2019. As Rongione points out, “there is only so long you can manage when revenue falls off 90 percent.”
Bollman managers created the BHC Cares Fund that raised $50,000 for hourly employees.
Guided by the firm’s core values, however, Rongione and his team are doing their best to provide for employees and steward Bollman Hat Company so that it survives for another generation. In addition to opening the factory to make masks, the Bollman managers created the “BHC Cares Fund” that raised $50,000 for hourly employees. The fund has provided each out-of-work employee with $250 cash and paid their portion of their healthcare premiums through May 16. The company is also looking for incentives to bring more workers back, for example, by offering an early payout of vacation days that would usually come after the July 4 holiday.
Asked if he can open the factory and make hats safely, Rongione replied unequivocally “yes.” The Adamstown factory has a half-million square feet, connected by catwalks and tunnels. After years of implementing LEAN production and eliminating “non-value-added handling,” Rongione says, the shop floor can be reconfigured to adapt to social distancing. Already, HR has developed a playbook to protect workers as they return.
The playbook includes training and handouts for workers on how to protect themselves as they return to the factory floor; implementing a morning screening routine, including questions about contacts and health; taking temperatures; and staggering start times, breaks, and lunches. Also, enhanced cleaning and disinfectant stations are in place. Says, Rongione, “We will phase in to ensure we can keep everyone in our building safe. If they do get sick, we’ll be making sure every employee can get the healthcare they need and have adequate time off to fully recover.”
The U.S. could learn from the experience of small manufacturers like Bollman Hat Company and another small manufacturer recently profiled in these pages, Opportunity Threads. Following the pandemic, we could lose more of our small, specialized manufacturers as we did after the Great Recession, or we could renew local manufacturing, create good jobs, and keep our supply chains closer to home. The Bollman Hat Company shows that with the right attitude—and some detailed planning—manufacturers can produce goods safely, even during a public health emergency. Rongione thinks employee ownership fits into the picture.
“As the U.S. awakens to our need to produce what we need to protect our people,” he says, “employee ownership is the oil that will grease the machine. With employee ownership, people care more and give more, and that ensures that more employers can make it through tough times.”
When profit is the only driver, we get outbreaks of COVID-19, as we see in giant meat-packing plants all around the country. When quality employment and stewardship come first, as it does with many employee-owned firms, we can put people back to work safely and allow our economy to grow again.
Karen Kahn is a communications consultant and the editor of Employee Ownership News.
To follow Employee Ownership News, subscribe to the Fifty by Fifty newsletter or follow us at Medium.