Carolina Textile District ramps up PPE production
by Karen Kahn
Health Care Workers in Need
One of the greatest failures as a nation, in the face of the coronavirus pandemic, is our inability to protect our health care workforce. We are all hearing stories of doctors and nurses on the frontlines without adequate personal protective equipment (PPE)—i.e., face masks, gowns and other protective gear. Other health care workers—including home care aides—also need PPE to continue to do their work safely and avoid infection.
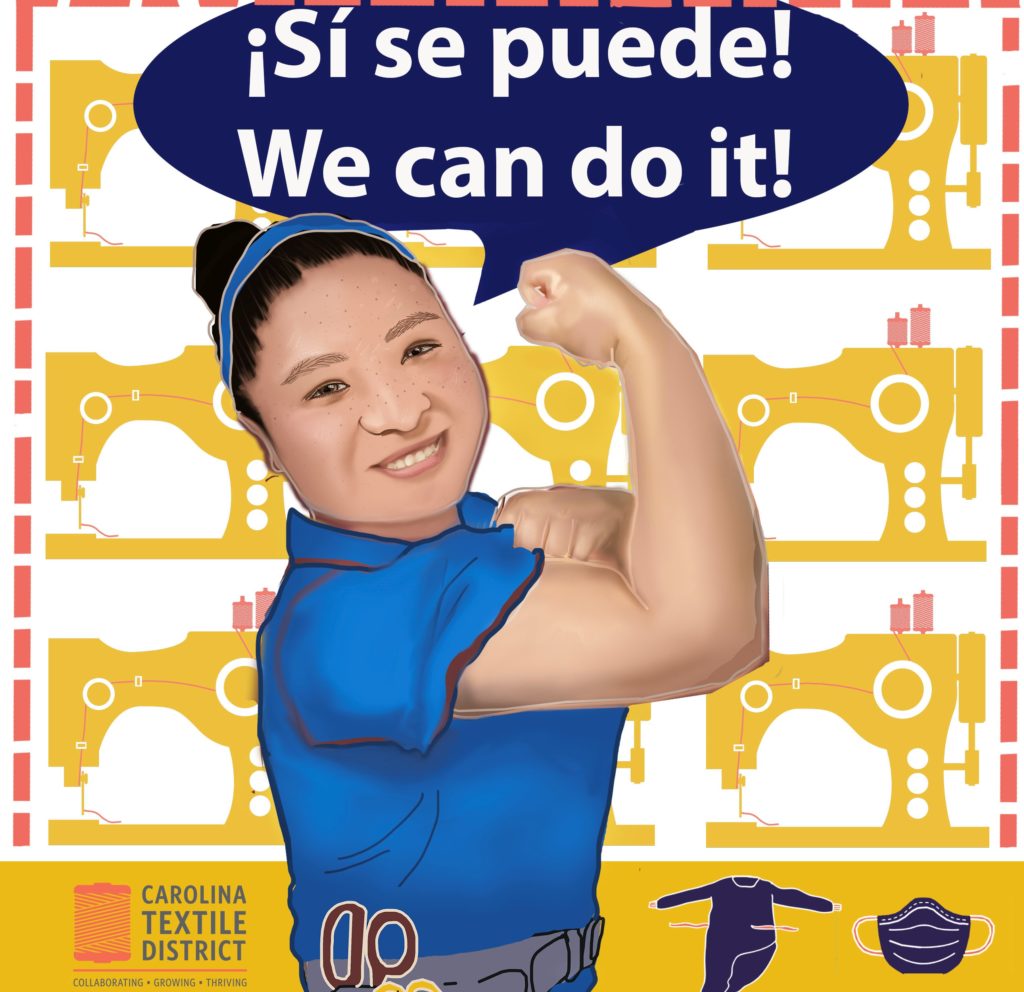
The nation’s largest worker cooperative, Cooperative Home Care Associates (CHCA), is smack in the middle of the U.S. epicenter—New York City. Its 2000 home health aides have been worried about visiting clients without the proper protective gear. Now another worker cooperative, Opportunity Threads in Morganton, NC, is coming to the rescue. Opportunity Threads began shipping face masks to CHCA the last week in March. According to Adria Powell, president of CHCA, the agency will need 1500 washable masks per week.
“We are igniting the economy we have been building for many years—unleashing its power to produce these items safely, and at the same time, saving jobs in impoverished rural communities.”
–Molly Hemstreet, co-director of The Industrial Commons and founder of Opportunity Threads
Textile Manufacturers Retool to Make PPE
Until recently, Opportunity Threads, a worker-owned cut-and-sew manufacturer, produced soft goods such as blankets and pillows and custom-designed apparel. The co-op’s worker owners are primarily Mayans who have immigrated from Guatemala to the hills of North Carolina. Opportunity Threads is a founding member of the Carolina Textile District, a cooperatively run network of textile manufacturers who have rebuilt local textile production in their region by developing locally based supply chains and distribution networks. These networks are now being put into service to produce PPE—for cooperatives like CHCA but also for Carolina health care workers. Products will include face masks, plastic face shields, gowns, scrubs, shoe covers, and hairnets.
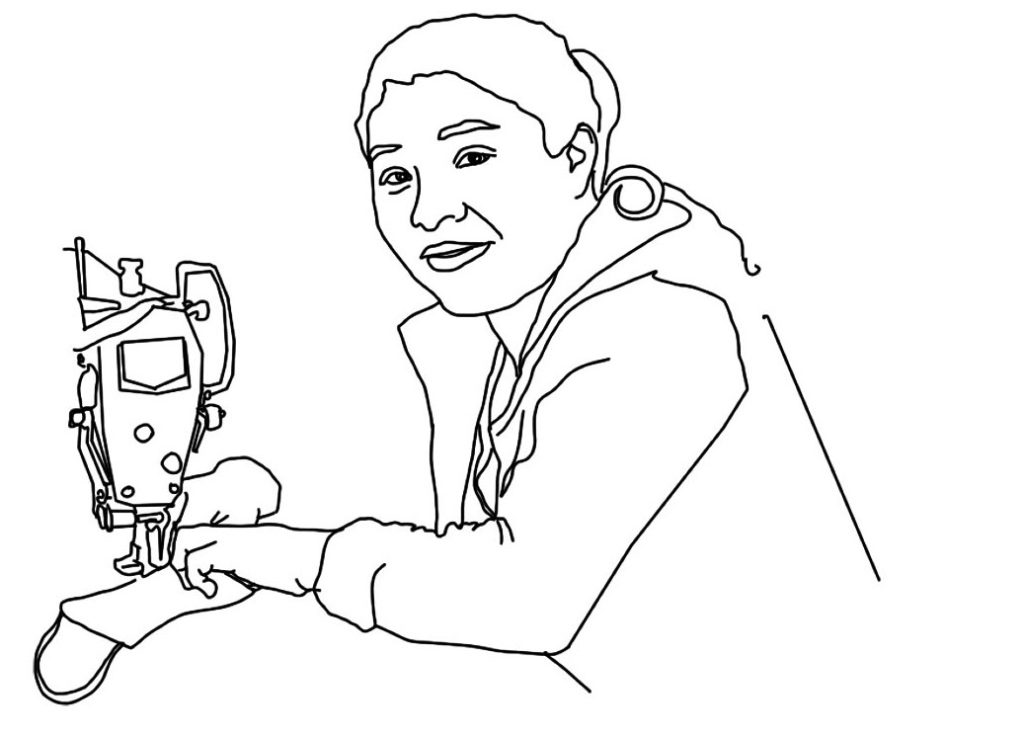
Molly Hemstreet, founder of Opportunity Threads and co-director of The Industrial Commons, the nonprofit affiliate of the Carolina Textile District (CTD), says that The Industrial Commons and its producers in the CTD were hesitant at first to switch production to PPE because of the multiple regulatory hurdles. They didn’t want to produce items that were not safe for health care providers. But it soon became clear that there was an overwhelming need, and that CTD was well positioned to meet that need. Moreover, switching to producing PPE would help to save jobs, since producers of these essential items cannot be shut down by “stay-at-home” orders.
To meet safety standards, the network brought in a team of medical doctors as advisers and is closely allied with an R&D facility where materials can be tested to ensure products meet all health and safety requirements.
A Story of Mutual Aid
Hemstreet and Powell have known each other for many years through cooperative networks. In mid-March, Powell was having a difficult time getting masks for her workforce. When she saw an article about sewers in Los Angeles making masks for health care workers, the light bulb went off and she decided to reach out to Hemstreet to see if the sewers at Opportunity Threads could become her supplier. The timing was perfect, as in response to local needs, Hemstreet was already in the process of developing prototypes. In the spirit of cooperative mutual aid, Hemstreet added CHCA to the list of priority customers.
The Opportunity Threads partnership, says Powell, will help CHCA manage the critical shortage of PPE, which has emerged since the COVID-19 outbreak.
The Opportunity Threads partnership, says Powell, will help CHCA manage the critical shortage of PPE, which has emerged since the outbreak of COVID-19, particularly since New York City is prioritizing hospital, nursing home, and EMS workers during this crisis. “With masks and other PPE, aides will be better prepared to manage concerns about contracting or spreading the virus as they care for their clients in the community and travel to and from their clients’ homes,” says Powell. “Also, we have 80 aides who are currently quarantined—i.e., exposed to someone who tested positive COVID-19 or exhibiting symptoms associated with the virus. The better we are at keeping everyone well protected, the less we have to worry about the spread of COVID-19 and the less disruptive it is to our ability to serve clients and support our workforce.”
Opportunity Threads must also keep its 50 sewers healthy and safe in the sewing factory. Hemstreet says they are taking extra precautions with sanitation and staggered lunch shifts, but in their 30,000 square-foot facility, everyone already works six to eight feet apart. Once thermal thermometers are available, workers will have their temperatures taken before they enter the workspace.
Precautions in place, Opportunity Threads is planning to produce 100,000 masks in the next 10 to 14 days. As production ramps up across CTD, the goal is to produce tens of thousands of masks, gowns and other PPE products. All items will be provided to local health workers and cooperatives like CHCA at cost. Says Hemstreet, “We are not trying to make a profit, just to keep our businesses alive through this crisis.”
Unleashing the Power of a Trusted Producer Network
Despite the enormous challenge of shifting local manufacturing from furniture, clothing, and other consumer goods to PPE, Hemstreet explained in a phone interview, CTD was well positioned to move quickly. “The network is used to working together, and there is a great deal of trust,” she said. “We are igniting the economy we have been building for many years—unleashing its power to produce these items safely, and at the same time, saving jobs in impoverished rural communities, which will help our long-term economic recovery.”
Almost immediately, with help from The Industrial Commons, CTD set up an intake system to determine the level of need and the capacity of manufacturers in the region to meet that need. In addition to the 250 sewers in CTD, another 200 companies with more than 1000 sewers signed on immediately to produce PPE.
CTD’s expertise in sourcing materials has been critical to the speed at which they have retooled. Hemstreet says, “Factories are going offline, so we have to move quickly to secure supply lines. For small manufacturers, writing big checks is difficult. But the CTD with its nonprofit sponsor, The Industrial Commons, can purchase the necessary materials.”
The Industrial Commons is setting up an e-commerce site for producers. Depending on their capabilities, a producer may purchase raw materials or sewkits that have the patterns already cut and ready to sew. They can also choose to produce product for CTD or to sell directly to their local health care centers and workers. The flexibility will allow for faster and more efficient production and distribution.
E.J. Victor, a high-end furniture manufacturer partnering with the CTD, has donated 20,000 square feet for a staging area, where raw materials will be housed and a fulfillment center will pack and ship finished goods.
Spotlight on Benefits of Local Manufacturing
The crisis is exposing the consequences of global supply chain disruption and the need to better support U.S. manufacturing and U.S. supply chains. “There hasn’t been much support for building domestic capacity, but now we can see why it is so important,” says Hemstreet. “It is worth paying a little more to ensure local capacity to produce critical items such as medical supplies.”
The crisis is exposing the consequences of global supply chain disruption and the need to better support U.S. manufacturing and U.S. supply chains.
Local production also encourages innovation. CTD is experimenting with new materials and washable PPE. “A single health system in North Carolina uses 400,000 gowns a day,” says Hemstreet. “Producing safe, washable PPE could be a much better use of resources.”
For the CHCA home care aides, washable masks are perfect. Unlike doctors and nurses who may be moving quickly between patients—and need new protective wear to prevent spreading infection—home care workers at CHCA see a limited number of clients per day. With their own washable masks, Powell says, they can make fewer trips to the office to get new supplies, avoiding putting themselves or others at risk on public transportation.
Powell is proud of CHCA’s workers, who, along with hospital workers, are heroically staffing the frontlines of this crisis. “The one silver lining,” she says, “is that this crisis has the potential to elevate the visibility of home care aides and the critical role they play in our health care systems.”
“We are truly grateful to the workers at Opportunity Threads,” she says, “who are making it possible for our workers to continue to go out every day and care for the most vulnerable residents of our city during this pandemic.”
Editor’s note: To help support this monumental effort to produce masks for CHCA workers and to expand the production of PPE for frontline medical workers, donate to The Industrial Commons. Donations specifically for CHCA should be marked “cooperative home care worker support.” It costs $13.50 to produce a pack of masks to protect a CHCA worker for one month.
Karen Kahn is a communications consultant and the editor of Employee Ownership News.
To follow Employee Ownership News, subscribe to the Fifty by Fifty newsletter or follow us at Medium.